Selecting the Right Magnet Wire Gauge for Efficiency
2023-12-12
Selecting the right magnet wire gauge is crucial for optimizing the efficiency of an electrical system. Magnet wire, also known as winding wire or enameled wire, is commonly used in the construction of coils, transformers, motors, and other electromagnetic devices.
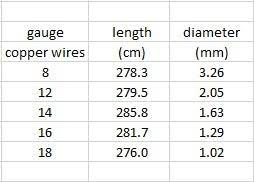
The choice of wire gauge affects the electrical resistance, heat generation, and overall performance of the system. Here are some factors to consider when selecting the right magnet wire gauge for efficiency:
Current Carrying Capacity:
Choose a wire gauge that can handle the expected current without excessive heating. The American Wire Gauge (AWG) system is commonly used to express wire sizes, and larger AWG numbers represent smaller wire diameters. Higher current applications generally require thicker wire (lower AWG).
Resistance:
Lower gauge wires have lower resistance, which reduces power loss due to heating. However, it's important to strike a balance because using excessively thick wire may increase material costs without providing significant benefits.
Voltage Drop:
Consider the length of the wire and the voltage drop along its length. For longer wire runs, thicker wire may be required to minimize voltage drop, especially in low-voltage applications.
Temperature Rating:
Check the temperature rating of the magnet wire and ensure it can withstand the operating conditions of the device. Operating at temperatures close to the wire's limit can reduce efficiency and lead to premature failure.
Space Constraints:
If space is limited, choose a wire with a smaller diameter. However, be mindful of current-carrying capacity and heating considerations.
Insulation Type:
Different insulation materials have varying thermal properties. Ensure that the insulation is suitable for the application's temperature requirements.
Cost Considerations:
Thicker wires are generally more expensive. Evaluate the trade-off between the initial cost of the wire and the long-term operating efficiency.
Skin Effect:
At higher frequencies, the skin effect can cause the current to concentrate near the surface of the wire. Thicker wire may be necessary to mitigate this effect in high-frequency applications.
Regulatory Compliance:
Consider any industry standards or regulations that may dictate specific wire gauges for safety and performance reasons.
Duty Cycle:
If the device operates intermittently, the duty cycle should be considered. Higher duty cycles may require thicker wire to handle increased heat generation during prolonged operation.
Always refer to the specific requirements of your application and consult relevant standards or guidelines. It's often helpful to perform calculations or use online tools to determine the optimal wire gauge based on the expected current, length of the wire, and other relevant factors. Additionally, seeking advice from electrical engineers or professionals in your specific industry can provide valuable insights.